What You Need to Know for Successful Product Selection
Even the simplest structures require the right materials for the job. But, like every part of the construction process, selecting and installing these materials is more complex than it might appear. A high degree of thought, experience, knowledge, and skill is required to ensure the project in question is built for durability, longevity, and aesthetic value. For those of us in the glazing trades, this means being able to not only evaluate plans and specs in order to install the most appropriate materials effectively, but also to solve engineering problems, identify potential issues with building codes, and adhere to manufacturer instructions.
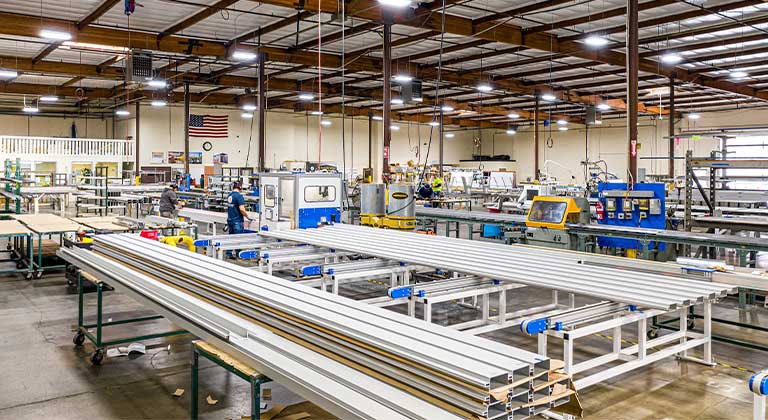
Our team at Giroux Glass has its own approach to material selection, assembly, and installation. When submitting a bid proposal, our estimators look at the building plans and specs and assess which materials will be required for the job, and from which manufacturer they’ll be sourced. In larger commercial projects, the preferred manufacturer is usually specified, but in luxury residential or retail projects, our team is often given more flexibility to select a manufacturer. In some cases — like design assist or design build, where we serve a more collaborative role — we might actively consult on which materials to use, and can choose our preferred supplier. In such cases, our selection often comes down to relationships. While there are countless manufacturers creating excellent glass and glazing materials, we’ve developed longstanding, ongoing professional relationships with a select few. These are the partners we can count on to deliver on their commitments. When given the chance to involve them in a great project, we take it.
Once a bid proposal has been accepted, our team can get more concrete about which vendors and materials to use for the project. At this stage, potential design issues may become apparent. Perhaps a storefront window is too large to support its surrounding structure, or maybe the architect’s plans left out fire-rated glass where the state requires it. It’s our job to identify these issues before ordering materials, to prevent bigger problems later. We might consult with third parties as well, depending on the unique specifications of the installation. For example, we may employ a structural engineer to help us assess what type of glass to use in a custom window system, or contact local agencies to discuss updated coding criteria. We need to confirm every aspect of our project scope before placing a material order.
When it’s time to order materials, it’s essential for us to also consider lead times and how they’ll affect scheduling and sequencing, especially for installations that are more intricate or customized. Custom doors and operables, for example, might take as long as 16-24 weeks to arrive once an order is placed. Our project managers and superintendents work together to make sure the project schedule is aligned with the material deliveries. This is especially crucial when factoring in challenges such as unanticipated extended lead times from vendors. As always, communication is key and our personnel are mandated to keep clients informed as soon as we become aware of any delivery delays.
Finally, we must be meticulous with material assembly and follow manufacturers’ directions to the letter prior to installation. This ensures that our work is built not only to last, but also to maintain the material’s warranty. If, for example, a window leaks due to improper assembly, that window’s warranty will be voided; it’s definitely a situation we want to prevent in every installation we complete.
To ensure that we build everything to the highest quality standards, our team holds internal “pre-activity” meetings and overviews everything from scheduling to assembly technique, to delegation of responsibilities. It also helps that the majority of our superintendents have been working with our company for over 15 years. Having experienced people you can count on is perhaps the greatest guarantee of quality performance for any company. We’ve been fortunate to cultivate a team of shop, field, and office personnel who value excellence in all projects, and our approach to material selection, assembly, and installation reflects their high standards.
This article originally appeared in USGlass magazine, volume 56, issue 8, August 2021