
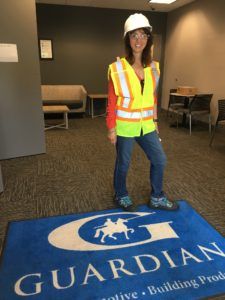
Guardian Glass is Guardian Industries’ largest of several divisions, and one of the world’s largest manufacturers of float, value-added and fabricated glass products. With twenty-eight float plants spread across five continents and twenty-five countries, I was fortunate, last month, to tour one of their more local facilities in Geneva, New York.
My tour guide was Mark Rice, customer account manager, who started working production with the company when the Geneva facility opened in 1998. Mark walked us through the process, at times popping us inside and back outside, to either escape the rain, or the intense heat in some of the oven areas, respectively.
I had never before seen floated glass being made, and as an admitted manufacturing-process nerd, I loved seeing all of it and did stop him often to ask many questions. Mark patiently answered all of them while we clocked the many steps needed to cover most of the building’s 850,000 square feet.
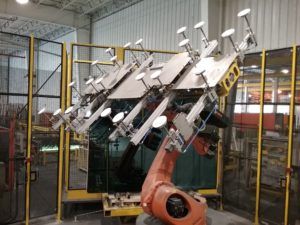
About fifteen years older than Giroux Glass, Guardian Industries began as the Guardian Glass Company in 1932, making automotive windshields. They opened their first float glass plant in Carleton, Michigan, in 1970. Today, Guardian Industries Corp. is a diversified global company headquartered in Auburn Hills, Michigan, manufacturing float glass and fabricated glass products for commercial, residential, technical and transportation applications; automotive trim; and providing distribution of building products.
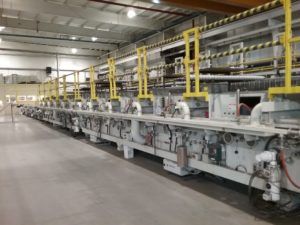
I was first impressed by seeing a long row of vending machines full of tools and supplies, made by Fastenal, that work with employees’ ID badges, dispensing needed items while tracking inventory. Prominently displayed next to these were regularly-updated charts showing production, logistics and safety metrics for everyone to see – all while still in the plant’s entry area.
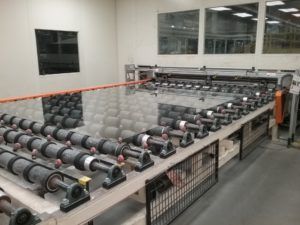
My first glimpse of glass was in one loading area, where large trucks parked in a deeply-sunken bay area were loaded by small cranes at floor height– preventing the need to hoist the glass dangerously high in the air. Mark explained that the biggest glass sizes made here measure an impressive 130 inches x 204 inches (or 10.8 feet x 17 feet).
Guardian glass can be found in homes, offices and cars and in some of the world’s most iconic buildings. I found it fascinating to see each step of its creation, with a new-found and deep appreciation for the workers who produce this ubiquitous material. The environment is loud enough to require ear-plugs, some areas are uncomfortably hot, and the plant never closes. I learned many interesting facts about the process, including:
-
A close-up view of the float line. The fluid that molten glass floats on is a bath of liquid tin;
- A diamond-encrusted wheel is used to seal edges of tempered glass, instead of a sander, kept wet the entire time (for those who mistakenly think there’s no bling in this process!);
- Mountains of broken pieces of glass are called “cullets;”
- The furnace at the “hot end” runs at 2700 degrees Fahrenheit, and this feels very hot, anywhere close to the area;
- The distance from start to end of the process is about a quarter of a mile;
- The Geneva plant floats about 700 tons of glass each day;
- The bigger the glass, the more cool-down time it requires, and cooling stresses the glass.
Long pieces of glass roll continuously along the float line.
Guardian Glass manufactures products for the commercial (Guardian SunGuard advanced architectural glass), residential (Guardian ClimaGuard), interiors (Guardian InGlass, Guardian ShowerGuard, DiamondGuard), automotive and technical glass industry segments. Its products include both float and value-added coated glass-products, such as tempered glass, low-emissivity (low-E) glass, mirrored and patterned glass, solar glass and insulating and reflective glass for a wide range of construction projects.
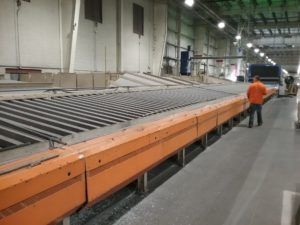
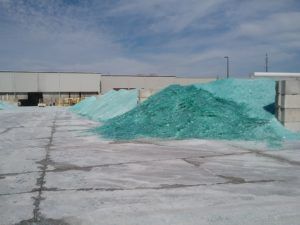
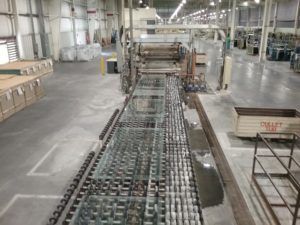